The global pharmaceutical glass market:
Most vaccines are packaged in borosilicate glass, the benchmark of good quality glass for drug delivery. COVID19 vaccine manufacturers require some very specific properties from their vials as many vaccines need transporting at extremely cold temperatures. Borosilicate glasses’ ability to withstand a range of temperatures from -200℃ to +500℃ makes it the perfect choice to meet this need. As a result, growing applications for high quality neutral borosilicate glass from the healthcare sector have now been compounded by unexpected and astronomical demand from the pharmaceutical industry as part of the ongoing global vaccination campaign against COVID19. With demand sky rocketing, the glass manufacturing industry has a tall order to fulfil.
In response, the glass industry is moving at speed to commission, design, build and fire up glass manufacturing facilities around the world, using the latest technological innovations to simultaneously improve plant efficiency, cost, performance and sustainability. To date, Glass Service Italy (GS) has installed 14 furnaces in Belarus, Iran, China, Russia, Pakistan and India. This case study highlights one of these furnaces that was already in the planning process when the pandemic hit and remarkably was completed despite the resulting chaos. Unfolding in Chongqing, China, and featuring the latest glass melting technologies, this study showcases both the specific challenges of pharmaceutical glass manufacturing and what’s possible when a bespoke, energy conscious approach is taken.

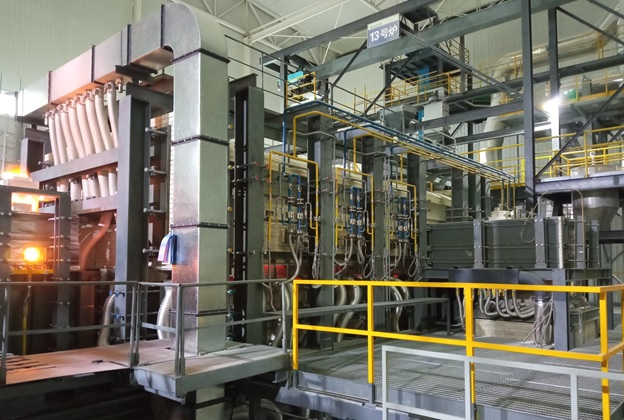
The client: For more than 18 months now, Glass Service Italy has worked hand-in-hand with a leading glass manufacturer, one that has produced more than 1000 billion Hydrolytic class II pieces of pharmaceutical glass, including vials and caps, all complying with YBB, ISO, EP, USP standards, as well as accreditation from CNAS. Recently, the client wanted to go one step further and level up production to Hydrolytic Class I to better meet their customer needs for volume and value. In order to achieve this they came to Glass Service Italy for help.
Client objectives: For this particular client in Chongqing China, the challenge was to help hit three specific macro targets:
1) Production of neutral borosilicate pharmaceutical glass tube alfa 51 to Hydrolytic Class I
2) Reduction of energy consumption by more than 50% compared to their existing furnaces
3) CO2 emissions reduced by more than 50% (reduction 2220 ton/CO2 per year)
Moreover there are further micro quality targets that glass manufacturers are consistently seeking to improve, including: stability across tube outer and inner diameters, consistent bending, vial thickness, absence of bubbles and stones and finally batch and chemical stability.
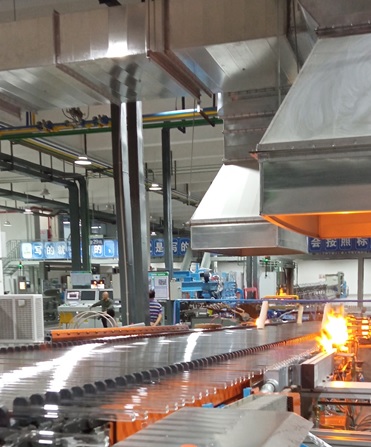
The specific client objectives on Hydrolytic I production and energy consumption represented a substantial change from the existing furnace infrastructure, and required support beyond the initial consultation, design and installation of a new furnace. To achieve new levels of efficiency, factors such as ease of maintenance, monitoring, furnace productivity and consistency of the output quality become even more crucial and for this, longer term support was essential.
In order to hit these targets the team set about addressing several factors that are particular to pharmaceutical glass production, including:
The unique challenges in manufacturing pharmaceutical glass:
- A very high melting temperatures of 1600℃ and the resulting increased energy consumption
- The greatly increased level of glass viscosity
- Elevated boron evaporation meaning increased corrosion rate of refractories in the chimney and waste ducts and increased silica salt knots in the glass
- Significant boron content volatilization impacting the thermal and chemical homogeneity of the glass.
- The instability of glass quality and the greater chance of batch pollution as a result of these factors
- The specific geometry of the site and the corresponding design of the melting tank.
Every client and every site is different and this is where Glass Service Italy comes into its own. With an expert team that is agile enough to design bespoke solutions for glass manufacturing clients, but large enough to have the experience, credibility and resources to tackle a project at any scale, they are well used to adapting cutting edge design to the specific needs of a client. To meet the client objectives whilst taking into account these considerations, Glass Service Italy experts created a customised furnace design and installation plan, combined with comprehensive training on the management, maintenance and testing of the equipment and its output for optimal performance and batch consistency.
Technical solutions for the Chongqing glass melting furnace:
The team began with key adjustments on the furnace design and features to ensure the delivery of both performance and quality targets.
The specific client objectives on Hydrolytic I production and energy consumption represented a substantial change from the existing furnace infrastructure, and required support beyond the initial consultation, design and installation of a new furnace. To achieve new levels of efficiency, factors such as ease of maintenance, monitoring, furnace productivity and consistency of the output quality become even more crucial and for this, longer term support was essential.
In order to hit these targets the team set about addressing several factors that are particular to pharmaceutical glass production, including:
The unique challenges in manufacturing pharmaceutical glass:
- A very high melting temperatures of 1600℃ and the resulting increased energy consumption
- The greatly increased level of glass viscosity
- Elevated boron evaporation meaning increased corrosion rate of refractories in the chimney and waste ducts and increased silica salt knots in the glass
- Significant boron content volatilization impacting the thermal and chemical homogeneity of the glass.
- The instability of glass quality and the greater chance of batch pollution as a result of these factors
- The specific geometry of the site and the corresponding design of the melting tank
Every client and every site is different and this is where Glass Service Italy comes into its own. With an expert team that is agile enough to design bespoke solutions for glass manufacturing clients, but large enough to have the experience, credibility and resources to tackle a project at any scale, they are well used to adapting cutting edge design to the specific needs of a client. To meet the client objectives whilst taking into account these considerations, Glass Service Italy experts created a customised furnace design and installation plan, combined with comprehensive training on the management, maintenance and testing of the equipment and its output for optimal performance and batch consistency.
Technical solutions for the Chongqing glass melting furnace:
The team began with key adjustments on the furnace design and features to ensure the delivery of both performance and quality targets.
Furnace design and features:
- Defining the right heating method for the melting tank, in this case using combined gas fire and electric power
- The optimal fuel: natural gas and oxygen are the natural choices here due to the high temperatures required
- Batch chargers: these machines and an inbuilt batch charger areas results in low dust, low boron evaporation, high machine life, glass stability and correct batch distribution
- Improving temperature control and glass homogeneity with water cooled bubblers
- Ensuring the quality of refractories for long furnace life
- Managing indirect heating in the working end and forehearths
- Incorporating surface drainage to remove glass defects
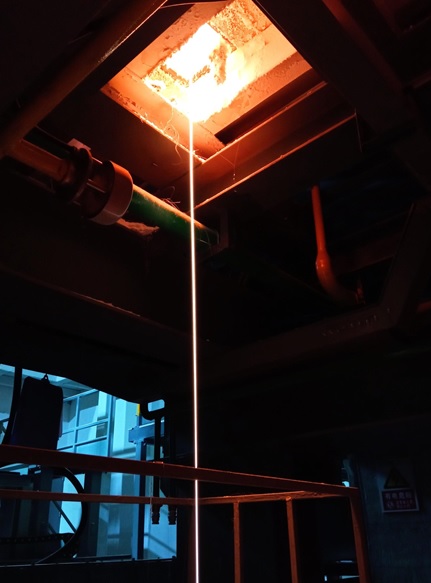
The furnace: Using these design features, Glass Service Italy’s team designed and installed an Oxy-Fuel furnace, producing 22Tons/24h of high-quality neutral borosilicate pharmaceutical glass tube alfa 51 – designed, engineered, assembled and commissioned in China. The team then remained on site until the production stage to help ensure batch consistency and production efficiency whilst guiding the client on the proper maintenance and performance management.
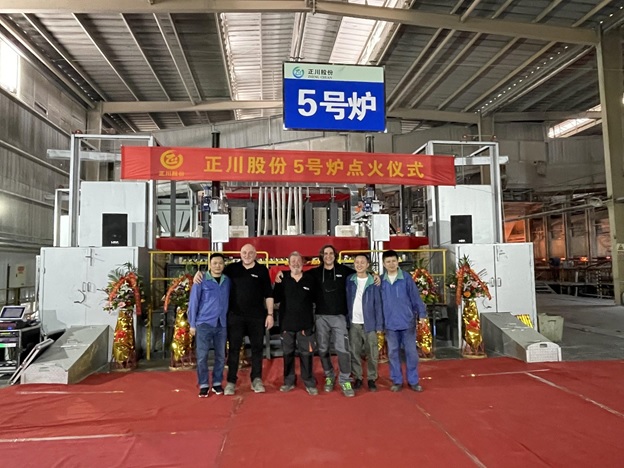
The opening ceremony: The time came to fire up the furnace in November 2020 and both the client and Glass Service Italy teams came together to mark the occasion with a ceremony to inspire good fortune for the plant and all those who work within it. Everyone gathered with confetti, celebratory banners and speeches as the furnace was fired up.
Process control system: a key part of successful furnace installation is the management, monitoring and maintenance of the machinery. Ensuring a consistent and high quality product and the health of the furnace is crucial for its long life. Process control systems that allow real time monitoring of the temperature, mass flow control, process control loops, alarm management and product accuracy, through an easy to use human machine interface (HMI) mean that monitoring the technology can be done easily by technicians with the right training.
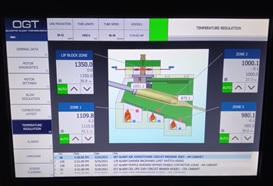
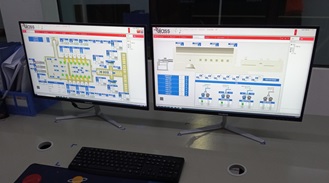
The results: The data speaks for itself. Efficiency: The tube diameter efficiency for this furnace is >80% on the 22mm diameter and the same for 16mm diameter with wall thickness efficiency of 100%! Energy consumption reduction: GS furnaces are lower consumption and meet both CO2 and cost reduction targets with energy consumption of 1250Kcal/kg fossil + 0.46 KWh/ kg electric booster
Future glass manufacturing focus: Glass is set to play a growing role in future sustainable development and has been pushed to the front in the battle against the Coronavirus. Key installations like this one in Chongqing are important in establishing glass’s movement towards a more sustainable, technology-led and efficient manufacturing model. Ongoing developments in end-to-end process management continue to reduce the amount of energy used by glass manufacturing and the renewed focus on plant efficiency, maintenance, monitoring and output quality, signals that there is much more to come from this area of the glass sector.